IMD-模內裝飾
In-Mold Decoration簡稱IMD,系指模內裝飾鑲嵌注塑成型,為一種在模具內注塑工件的同時,將已印刷紋路的膜料貼合或轉印在工件表面的技術。相較傳統的水轉印,模內裝飾技術能解決圖案在工件上對位的問題,紋路不易變形,且成品具耐腐蝕、高抗刮等特性,因過程更加環保,因此許多電子產品紛紛以 IMD 讓產品外觀增加多樣性,廣用於汽車內飾、家電面板、電子通訊機殼等產品上。
此項工藝又分為 INS(模內鑲件)、IMR(模內轉印)、IML(模內貼標)、IMF,以下為說明介紹:
1.INS (Insert Thermoforming film to Molding) 將印好的膜裁切後,直接射出或是加熱吸塑成3D型嵌入模穴中與注入塑料結合射出。2.IMR (in mold Rolling) 也稱平面轉寫、模內轉印,產品外觀受到高度曲面限制只能做微曲產品。
3.IML (in mold labeling) 平面一體成型技術,2D平面、印刷+沖切+射出。
4.IMF (in mold forming) 曲面一體成型技術,2.5D~3D立體造型、印刷+高壓+沖切+射出)。
INS-模內嵌片成型-介紹
INS是什麼?
即嵌片注塑工藝(Film Insert Molding)、利用熱吸塑成型或高壓成型的方法,把轉印好的膜材(一般是0.5mm厚)進行三度拉伸、然後依照產品外型裁出嵌片、接著在把此嵌片準確地置於注塑模腔內、注塑成型。INS膜片可與電子部件相結合,於INS膜片底部絲印透光紋理,利用燈光的明暗與色彩,造就不同的紋路圖案,呈現豐富的視覺效果。
INS簡易製作流程
INS的基材:材質主要是ABS、ABS/PMMA
薄膜(PMMA印刷+貼合ABS)
→加熱→吸塑成型→裁切成嵌片→埋入模具→射出注塑→成品
ABS UV壓紋上色
→加熱→吸塑成型→裁切成嵌片→埋入模具→射出注塑→成品

INS(模內嵌片)產品應用

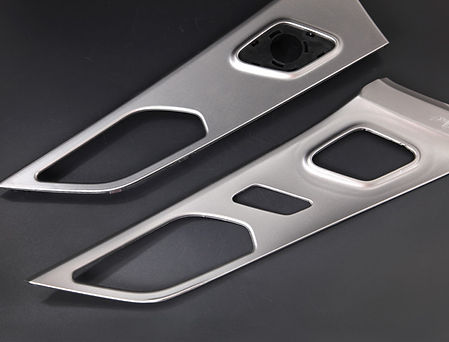

IMR-模內轉印-介紹
模內轉印 In Molding Roller,簡稱 IMR,是將設計好的紋路印刷於離形轉印膜上,並預熱離形轉印膜,真空成形後再射出成型,完成後有圖案的油墨會與薄膜分離,留下油墨與保護層,即完成具有紋理的工件產品。

IML-模內貼標-介紹
IML(模內貼標)是將印有圖形或標誌的貼合膜,於合模注塑的同時,將膜面貼合於注塑工件表面其成品相較傳統貼標,優勢在於標籤與塑料一體成型,能達到更完美的貼合。

IMF-模內鑲件-介紹
IMF適用於3D產品,其作法是將印好圖案的IMF膜,於高壓吸塑成型機裡預成型,再將預成型的膜裁切下來,嵌入注塑模具中,進行注塑即完成。其完成品分為上層硬化的透明薄膜(常見材質有PC、PET、PMMA等)、中間印刷圖案層,以及背面塑膠層,因油墨不同於前兩者均在產品表層,而是在產品中間層,這樣的技術更可確保產品極佳的牢色度與耐刮性。